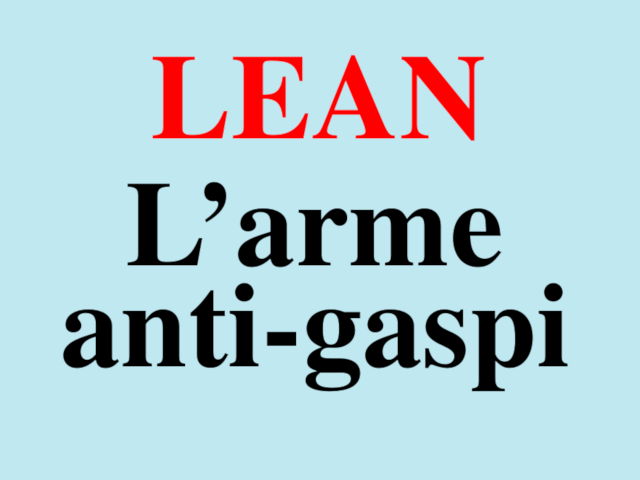
Le régime minceur venu du Japon arrivera- t-il à convaincre les industriels de l’agroalimentaire ? En ces temps de crise, il semble en tout cas gagner du terrain. Il faut dire qu’il dispose d’arguments de poids : réduction des coûts, amélioration de la qualité, augmentation de la productivité. De quoi š'agit-il ? Du Lean.
Le Lean, traduction de "maigre", est une
démarche née dans le secteur automobile,
inspirée du modèle Toyota. Son objectif est
de produire au plus juste et d’éliminer tout
ce qui n’apporte pas de valeur ajoutée : la
surproduction, les délais d’attente, les tâches
et les mouvements inutiles, la non qualité
... Cette démarche englobe
des techniques et des outils permettant d’éliminer les gaspillages et la variabilité, d’
améliorer la flexibilité des outils et des méthodes de travail, mais elle préconise aussi
une organisation du travail radicalement
différente, donnant une place beaucoup plus
importante à l’initiative des opérateurs et de
l’encadrement et visant à progresser ensemble
souligne le rapport réalisé en 2006
par Mc Kinsey Global Institute qui, dès 2006,
a préconisé le développement du Lean
comme levier d’optimisation des performances des entreprises.
Sur les traces de l’automobile, les
industries agroalimentaires, déjà
initiées aux démarches d’amélioration continue, semblent bien être
réceptives à ce type d’approche.
La démarche Lean, portée activement par
les sociétés de consulting il est vrai, fait des
émules dans tous les domaines industriels y
compris dans l’agroalimentaire. Autre particularité du secteur : les contraintes
réglementaires et d’organisation, notamment en matière d’hygiène et de propreté.
Mais quelle est donc l’origine de cette dé-marche qui fait l’actualité des spécialistes enorganisation industrielle ? Petit rappelhistorique : après la seconde guerre mondiale, Kiichiro Toyoda et Taiichi Ohno,
ingénieurs de production chez Toyota,
réfléchissent aux possibilités d’améliorer le concept de standardisation développé par Henri Ford afin d’assurer un flux continu ainsi
qu’une grande variété de produits. C’est la naissance du système de production Toyota (TPS) basé sur le juste-à-temps et les flux tirés.
Et puis, en 1990, trois chercheurs améri-
cains, James Womak, Daniel Jones et
Daniel Roos, décrivent dans le livre "The
machine that changed the world" l’efficacité du TPS rebaptisé alors "Lean" (maigre en anglais). Son principe : Le Lean serait-il alors l’apanage des
grands groupes ? Pas du tout, répondent
unanimement les experts interrogés qui pointent la souplesse des méthodes, leur étendue de la production aux services et l’importante des bénéfices potentiels. Ces principes étant posés, comment faire pour mettre en place cette démarche ? Le principe est donc d’identifier ces points noirs, de les analyser et de mettre en place
des actions correctives. La démarche s’appuie ainsi sur divers outils aux noms aussi
évocateurs que VSM, Smed, 5S, TPM,
Kanban... Ces derniers
concernent les flux et les processus, les
produits, la maitrise des opérations ou des
ressources, les hommes et l’organisation.
Tout serait donc si simple ? Pas sûr car le
chemin sur la voie de la performance est
souvent semé d’embûches. Tout d’abord, au
niveau de 1’organisation : pour être pérenne,
un projet Lean doit être porté par la
direction, et impliquer un chef de projet
qui assure cette activité transverse de métho-
dologie. Laurent Bénard, Françoise Foucher, Isabelle Gattegno
Toute entreprise qui veut s’améliorer de manière continue et pérenniser ses résultats a intérêt à entamer son parcours Lean », précise Gilbert Liégeois, président de l’Institut Lean France, association créée pour diffuser les bonnes pratiques de cette approche sur le territoire national. Le déploiement de la démarche Lean s’appuie sur la
mise en place d’ une palette
d’outils dont certains sont déjà
familiers aux IAA : 5S, TPM,
Smed...
Mais il ne faut pas
croire que si l’on implante un par
un ces outils, l’entreprise fini-ra
par devenir Lean. Le Lean nécessite un autre mode de pensée
et de management. C’est pourquoi
nous préconisons de commencer
par former les managers avant de
commencer à introduire les outils
,
tempère Gilbert Liégeois.
Une démarche Lean se doit d’ être lancée quand on est encore en bonne
santé financière. Les IAA, moins touchées
que d’autres par la crise, ont tout intérêt à
s’y mettre alors qu’elles en ont encore les
moyens. De plus, dans un environnement
anxiogène tel que nous le rencontrons actuellement, l’expérience montre que les salariés
sont prêts à se mobiliser massivement
autour d’un plan de recherche d’économies,
avec à la clé des résultats intéressants pour
l’entreprise
, remarque Philippe Delwarde,
D.g. du cabinet conseil Quaternaire. Une
mobilisation bien présente dans les
entreprises comme Danone, Marie, Les
Crudettes, Fromagerie Milleret qui se sont
lancées dans l’aventure Lean.Basé sur le bon sens, le Lean vise à produire au plus juste pour garantir la satisfaction du client tout en simplifiant les pratiques de fonctionnement. Explications.
Dans un
contexte de crise, les industries alimentaires
cherchent à retrouver des marges et se
tournent vers des méthodes qui ont fait leurs
preuves dans d’autres secteurs comme
l’automobile. Mais il existe des spécificités
propres aux IAA comme le manque de stan-
dardisation de la matière première ou des
temps incompressibles dans la fabrication
qui nécessitent de bien réfléchir à l’adaptation du lean pour pérenniser les démarches
, souligne Xavier Blais, spécialiste de la performance industrielle.
Il faut décloisonner les démarches et éviter
de déployer les outils du Lean à la marge
des systèmes de management de la qualité,
car cela conduit à générer de nouvelles
règles opérationnelles sans exploiter l’existant. Or il s’agit bien des mêmes processus
que ceux attendus dans le cadre de la norme
Iso 9001 ou de l’IFS dans une moindre mesure
, conseille de son côté Olivier
Dagoreau, directeur d’Exaris, cabinet d’expertise en analyse de risques.
Un vrai changement de culture
concentrer les énergies
sur la création de valeur pour le client en simplifiant les pratiques de
fonctionnement dans une approche coopérative d’amélioration continue et mobiliser l’ensemble des équipes autour d’objectifs de performance ambitieux. Il s’agit d’un véritable changement de culture dont la réussite passe par une très forte implication de la direction générale
, explique Frédéric Le Moigne, associé du cabinet Proconseil, et spécialiste du Lean dans l’agroalimentaire. Le Lean concerne toutes les fonctions de l’entreprise : la
production bien sûr (Lean Manufacturing) sur laquelle il s’est d’abord concentré mais
aussi les domaines marketing, commercial...
Chaîne de valeurs
Les opérations sans valeur doivent
être supprimées. Cette réduction du gaspillage peut ainsi devenir à terme un avantage concurrentiel pour l’entreprise
, souligne Bernard Tanous, dont le cabinet conseil propose un logiciel d’aide à l’optimisation des flux. Et cette approche Lean a d’autant plus de sens que le niveau de valeur ajoutée de 1’en- treprise dans ses transformations est important. Elle apporte donc des béné- fices en particulier dans des entreprises de fabrication de produits traiteurs et élaborés, abattage-découpe avec condi- tionnement, colisage ...
, poursuit-il.
Toutes les entreprises sont concer- nées par cette approche même s’il est vrai que les grands groupes dont les
dirigeants viennent parfois de l'automobile s’y sont intéressés plus vite
,précise Hubert Siegfriedt, directeur du cabinet Lean Training. Reste que le Lean est une vraie culture qui
nécessite un nouveau regard sur l’outil industriel autour des notions de flux, de valeur ajoutée.
Adopter une démarche Lean revient à adopter de nouveaux modes de fonctionnement. Aussi ne faut-il pas être dogmatique lorsque l’on souhaite déployer une telle méthode et s’adapter à la culture de l’entreprise. Dans un grand groupe structuré, on cherchera à homogénéiser les façons de faire à l’ ensemble des sites alors que
pour une PME, l’approche sera plus opérationnelle, plus pratique
, note Sébastien Caillau, directeur des opérations du pôle conseil d’Elcimaï,
dont la société va accompagner, à la demande de la CCI de l'Artois, six entreprises dans une démarche Lean, dont une du secteur agroalimentaire.
Par ailleurs, la mise en place du Lean dépend du type d’industrie. Ainsi, dans une laiterie ou le produit est en permanence dans des tuyaux, on ne regardera que très peu le process, à l’exception d’une démarche TPM (Total Productive Maintenance) et on se focalisera plutôt sur la collecte amont ou lalogistique aval
, poursuit-il.
80 % des délais, 50 % des coûts et 35 % des pertes de capacités sont le fait d’activités sans valeur ajoutée, celles pour lesquelles le client n’est pas prêt à payer c’est-a-dire des gaspillages, des dépenses ajoutées, de la non-valeur ajoutée
, explique encore Fréderic Le Moigne. II s’agit notamment des délais d’attente pour la mise en route d’une machine ou une prise de décision, de surplus de stock, de mouvements et déplacements inutiles, de non qualité, de surproduction...
Boîte à outils
Mais ces outils peuvent être soit ses
meilleurs amis s’ils sont bien utilisés et
permettent d’identifier les gaspillages, soit
ses pires ennemis si l’on se laisse aveugler
par ces derniers et que l’on oublie la
démarche globale
, souligne Sébastien
Caillau. L’analyse de la non-valeur soulève
de nombreuses questions stratégiques,
dont la rationalisation des gammes. II
s’agit notamment de mesurer l’impact sur
le plan industriel de la suppression d’un
produit non essentiel. En combinant cette
réflexion à une démarche Smed, qui permet
de diminuer les temps de changement de
formats, et avec la mise en place d’une
maintenance de niveau 1, n’arrivera-t-on
pas à gagner suffisamment pour décaler
des investissements, ou réduire ses stocks
et donc diminuer ses encours ?
, analyse
Philippe Delwarde, directeur général du
cabinet de conseil en management
Quaternaire. Management visuel et ap-
proche ludique peuvent être aussi pri-
vilégiés. Chez un de nos clients, nous
avons dessiné sur une bande de papier de
dix mètres de long, sa ligne de production
et 1’avons collée au mur. Puis, les équipes
terrain ont été invitées à y positionner des
post-it de couleur correspondant à un type
de perte (énergie, main-d’œuvre, produit,
etc.) et à mettre un commentaire sur ces
papiers. Le résultat a été excellent car cela
leur a permis de se projeter dans leur
environnement de travail habituel
,
explique encore Philippe Delwarde.
Des écueils à éviter
Or il n’existe presque jamais en
IAA de fonctions méthodes transverses
,
souligne encore Philippe Delwarde. Par
ailleurs, pour que la mise en place d’une
démarche lean s’accompagne d’effets significatifs, il s’agit d’éviter quelques écueils :
accumuler les micro-chantiers et perdre le
sens global de la démarche, ne pas communiquer suffisamment autour du projet,
ne pas être suffisamment transparent sur
les économies que génèrent les améliorations, ou même oublier de fêter avec les
équipes l’atteinte d’un objectif !